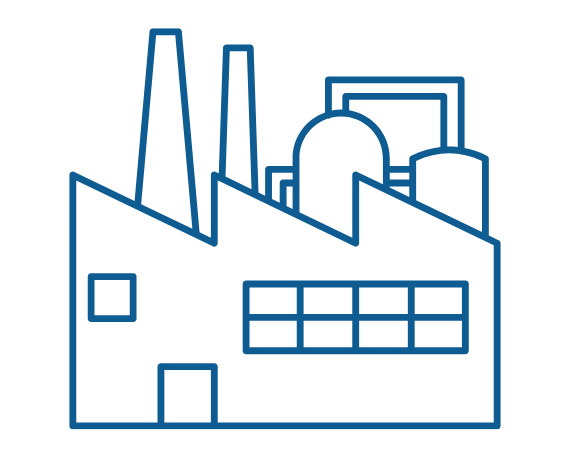
A bevy of manufacturing companies and executives have joined our Circles community recently. Why? We went to investigate. It turns out that sector has a head start dealing with trends that are now headlines for other sectors: scarcity of skilled hires, managing rapid change, and distributed work.
Connected to Close the Skills Gap
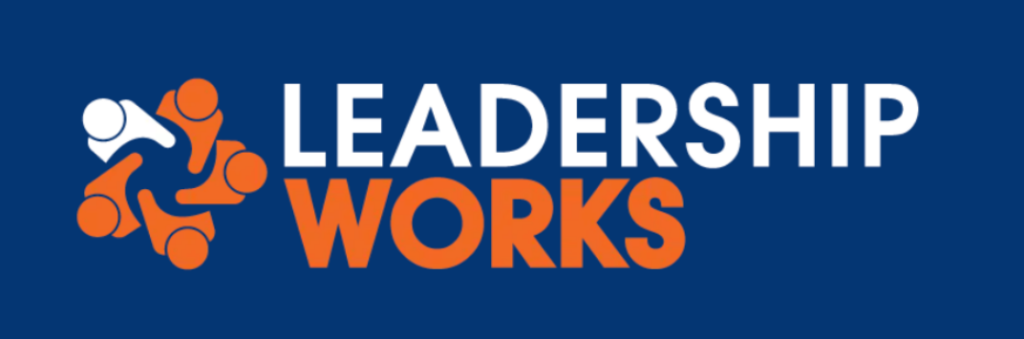
America Works is a manufacturing industry community that bridges the gap between the widening skills gap and labor supply. According to a Deloitte study, the U.S. manufacturing skills gap could reach 2.1 million by 2030.
Consultants in the community work with manufacturing companies to help them build a more capable, skilled, diverse workforce. Executive Director Matt Fieldman focuses on connecting these consultants to each other and to best practices and resources that can help.
One example of a successful program is TechCred, where “The state of Ohio keeps a list of 400 plus credentials through the TechCred program, where the state reimburses manufacturers for training.” He also organizes FireWorks, an annual conference gathering America Works consultants together. Recently, Matt partnered with Circles to connect Leadership Works participants in peer circles between conferences. “Circles sessions are not tactical; it’s a support network aimed at focusing more on personal challenges. They tend to form deep relationships right off the bat.”
Leadership Works Circles participants shared that they had previously “struggled to meet industry colleagues” and that the sessions provide “a new opportunity to meet with my peers and exchange concerns, ideas and solutions.” Matt’s takeaway is that rapid change and automation only increases the need for connection. “Human connection still matters, and manufacturing professionals need to connect with each other now more than ever.”
Connected During Rapid Change
Automation, offshoring and then supply chain disruptions and a rush back to domestic manufacturing have made rapid change the new normal for many manufacturers. Manoeuvring through constant transition requires skilled leaders at every level. A small team of divisional leaders sparked a grassroots movement to address this at Dupont. They worked with Circl.es to create a custom program titled, “Navigating Change Together.” Individuals invited other team members across regions & functions to process in virtual small groups and journey through three new curated, facilitated, 90-minute sessions.
Participants shared personal motivations for joining:
“It’s been difficult to cope with the constant change in DuPont the last five years.”
“It’s more important than ever that we respectfully communicate, trust and support each other.”
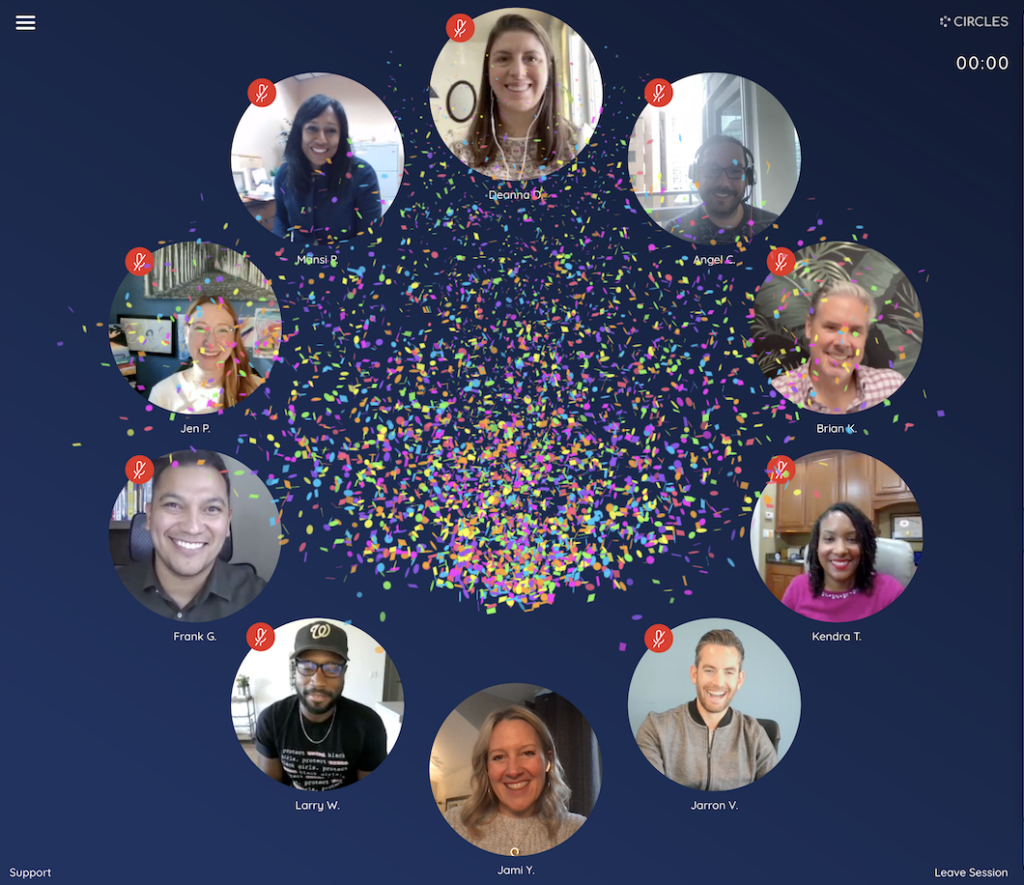
The facilitated NCT discussions forged stronger connections and helped DuPonters harvest their collective strength, build trust and belonging, and find ways to help each other thrive. By connecting on a deeper level, the program acted as a lifeline and buoyed them through the organizational changes.
Building Leaders at Every Level
Most U.S. manufacturing companies are small, family-owned businesses of less than 500 employees, and Pennsylvania’s Electri-cord is one of them. Owner Mitch Samuels has always believed that “learning and leadership are indispensable to one another” and has lived through Young Presidents’ Organization’s (YPO) small group Forum for years. Mitch shares that “Forum has changed my life in so many ways, through networking and peer connection.” His positive Forum experience over many decades prompted him to recently nominate his sons for Key Associates Forum, a program that YPO launched with Circl.es earlier this year. Now, his two sons Jason and Ryan, heads of Business Development and Sales and Marketing, rely on peer connections in Forum powered by Circles to develop the leadership skills they need to handle rapid changes. Jason recalls, “When I was young I remember thinking that my dad’s Forums were just another business meeting. Now I understand firsthand how important it really is.”
Ryan describes Circles as a unique experience that lends itself to forum and open conversation, through a combination of facilitator, platform and program. “KA Forum sessions are two hours long, and I always leave feeling like there was more that we could have said.” Both Jason and Ryan have noticed an impact in the way they think about and lead their respective divisions at work, and consider it an investment in their family business and the manufacturing industry for generations to come.
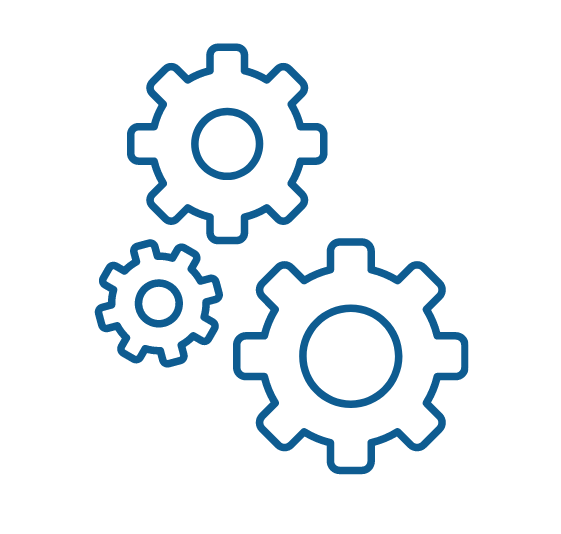
At the other end of the size scale, Stryker, one of the most respected names in manufacturing, came to a similar conclusion. They partnered with Harvard Business School, (HBS) to support their rising leaders. Like YPO, HBS also partnered with Circl.es to develop the small-group, cohort-based aspect of their development program.
Connected Across Distributed Teams
Paula Tewksbury has worked in manufacturing for 30 years and knows the value of maintaining connections across distributed peer teams. “Change is always happening, and plant managers never get to connect and network with peers, so our middle managers often don’t have anyone to bounce ideas off of. I immediately saw how Circles promotes employee engagement.”
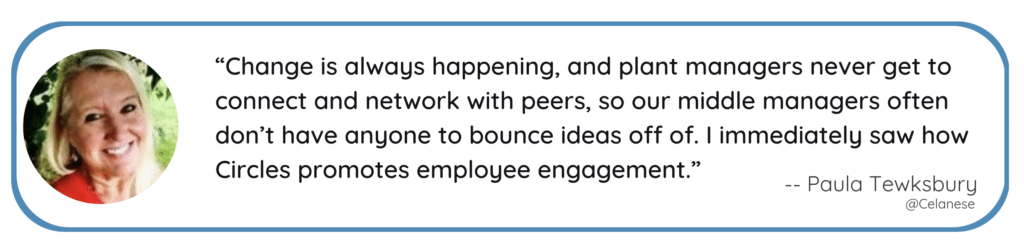
Paula participated in a circle, then became a facilitator, and finally helped design sessions for employees. She had previously tried other learning & development tools and training, and noticed Circles was different because it allows leaders to grow and develop in facilitation skills, an area Paula has personally participated in for decades. “By design, Circles helps individuals grow in facilitation, while connecting them to other leaders across silos.” She feels connection in circles will upskill manufacturing employees in strategic ways that will buoy them through rapid industry change.
Conclusion
One reason we’re writing this article is to draw attention to the small group approach as a way for other manufacturers to address their workforce challenges. However, in a world where other sectors face automation, distributed work, and rapid change, this approach is universally applicable. Plants and office buildings may be increasingly “lights out” but humans are required more than ever, and humans are at their best in small groups.
In addition to industry hurdles like automation, the skills gap and upskilling, the real challenge is the disconnection manufacturing employees face at all levels. Whether it’s executives, consultants, plant leaders or manufacturing professionals, the entire industry benefits from human connection in Circles.